Organizing the choke points
IT TOOK the United Parcel Service 108 years to get to its current position in the world today, less than half that time for Walmart, DHL and FedEx, and just over two decades for Amazon. The speed of transformation in the global logistics industry is rapidly increasing, spurred on by Amazon's current building spree across North America and Europe.
For example, according to Business Insider:
Amazon has added 21 new logistics facilities globally over the last 12 months, up 14 percent from last year, bringing the total to 173 facilities worldwide. Of the 173 facilities, 104 are in the North America region, with the rest spread across Europe and Asia. The 173 logistics facilities include the large fulfillment-center warehouse; sortation centers, where packages get presorted for shipping; and Prime Now hub, a separate building to store one-hour delivery items.
Clearly big things are afoot. Amazon's recent job listing strongly suggests it is building a senior staff for a major logistics and transportation department that includes a "Senior Program Manager--Last Mile Transportation SME," "Driver Experience Manager," and "Network Manager--Amazon Logistics Freight." A former Amazon engineer told Business Insider, "If Amazon can stop paying FedEx and start controlling their own destiny in terms of the costs of fulfillment and shipping and transportation, it increases their profit margin."
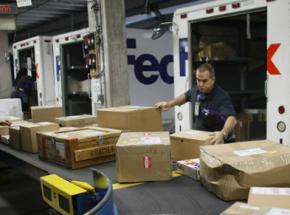
Another sign of the rapidly transforming logistics industry is UPS's recent purchase of the Chicago-based Coyote Logistics for $1.8 billion. Coyote is a new model of freight forwarding; it has no vehicles or warehouses of its own, and instead provides logistics for 12,000 shippers with a network of 35,000 local, regional and national carriers.
A decade earlier, UPS made its largest acquisition up to that point when it bought Overnite Transportation, a huge nonunion freight company. UPS's purchase of Overnite was a major move into the traditional freight business, and followed FedEx's acquisition of several regional freight companies and creation of FedEx Freight.
FedEx is also trying to keep up with the competitive pressures from Amazon and UPS. Earlier this year, it acquired the Dutch parcel-delivery company TNT Express for $4.8 billion--giving it access to TNT's Europe-wide road network to compete with UPS and DHL--and FedEx Ground has announced plans to build large facilities in Middleton, Connecticut; Ocala, Florida; and Hamburg, New York.
DHL--formally DHL Express, a division of Deutsche Post--is also reinvesting substantially in its U.S. operations, including a $108 million upgrade to its Cincinnati air hub that processes about 46 million international shipments each year. Though it is smaller than UPS's nearby Worldport or FedEx's Superhub, DHL's Cincinnati operations primarily focus on international shipments from Asia and Europe.
"If DHL is making investments in infrastructure expansion in Cincinnati, that means they're very confident that they're going to continue to grow their intercontinental network," says Brian Clancy, a managing director with Logistics Capital & Strategy, a Virginia-based transportation consulting firm.
MEANWHILE, DHL Global Forwarding signed an agreement with a Kazakhstan-based express company to speed the transit of rail-based freight across the Eurasian continent as an alternative to traditional sea and airfreight. In addition, it announced plans to establish its own parcel network in Austria by 2016 and to invest €47 million in sub-Saharan Africa as part of an effort to derive 30 percent of its revenue from emerging markets by 2020.
Not to be left out of the scramble, the United States Postal Service (USPS), the venerable, much-derided and constitutionally mandated mail carrier, has emerged as a major player in the logistics industry.
This summer, Bloomberg Businessweek called the USPS "an extension of Amazon" and noted that "Amazon receives a deep discount from the post office because the e-tailer does so much of its own processing--including providing computerized address lists to make it easier for carriers to tailor their delivery routes for faster drop-offs." A 2014 estimate by Bernstein Research, which tracks the shipping industry, put the USPS's shipments and deliveries at 40 percent of Amazon's volume, or almost 150 million items (UPS accounted for 20–25 percent and FedEx 15–20 percent).
While UPS, FedEx, DHL and the USPS are fierce competitors, many people would be surprised by the cooperation between the logistics giants. Both FedEx and UPS have discounted residential package delivery services with the USPS, called, respectively, SmartPost and SurePost. And the volume is enormous. Last year, the Wall Street Journal reported:
For FedEx alone, the post office delivers an average of 2.2 million packages a day, or about 30 percent of the express-mail company's total U.S. ground segment. UPS won't specify how many of its shipments go through the post office, but a regulatory filing indicates those types of lightweight shipments accounted for 40 percent--or about 37 million packages--of its total increase in ground shipments in 2012.
Both SmartPost and SurePost services are designed to deal with the unwanted costs of the "last mile"--the industry term for the final step in the delivery process, handing over the package to the recipient. FedEx or UPS may have every address in the United States in their databases, but neither wants to go to every address every day, and they certainly don't want to make a second attempt if the recipient isn't home the first time around. The USPS, on the other hand, has to go to each address daily to delivery first-class mail.
Ultimately, UPS and FedEx want to snatch up the most profitable areas and dump the rest. For example, FedEx beat out UPS in 2013 for a seven-year, $10.5 billion contract with the USPS to fly its mail between U.S. airports.
The rising volume of packages has transformed the USPS, necessitating major capital investment. In 2013, the post office spent $200 million to furnish its delivery vehicles with handheld scanners to provide real-time package tracking. And its plan to replace its fleet of 163,000 delivery trucks, which were not designed to hold packages, could cost as much as $4.5 billion.
WHILE GREG Niemann once boasted that "UPSers turn out better than machines," that hasn't stopped the company from trying to turn its workers into cogs in the machinery. Harry Braverman examined the intertwining forces of new technology and scientific management in shaping the modern factory for maximum profit, but his approach is easily applicable to the daily grind of package car drivers today:
The physical process of production are now carried out more or less blindly, not only by the workers who perform them, but often by lower ranks of supervisory employees as well. The production units operate like a hand, watched, corrected, and controlled by a distant brain.
Braverman's observation describes Orion--UPS's new routing program, whose algorithm is 1,000 pages long and was designed by 50 UPS engineers--perfectly. According to UPS, Orion "uses expansive fleet telematics and advanced algorithms to gather and calculate countless amounts of data to provide UPS drivers with optimized routes." Drivers once valued for their route knowledge have been reduced to little more than implementers of a software program that contains the 55,000 daily package car delivery routes across the U.S.
Telematics, once understood as the application of computerization to fleet management, has morphed into something much broader. "Arguably one of the very first companies to employ analytics to improve operations," Data Informed writes, "over the last 15 years UPS has moved from simply describing what happened yesterday to predicting and prescribing how it will operate tomorrow."
This has made the driver's life hell, journalist Jessica Bruder writes:
Now drivers were called to account for a litany of small sins. They were asked to justify bathroom breaks and any other deviations--"stealing time" in corporate-speak--that could chip away at their SPORH (pronounced "spoor") count, or Stops Per On-Road Hour.
Another driver told her:
I have no problem doing a heavy, hard job...But now, after you do the job, you have to look back every day and say, "Did I do this? Did I do that?" They have a report that tells them everything that you did wrong. For instance, if you turned the truck on before you put on your seat belt, that's wasting gas.
A former driver described the purpose of this succinctly: "Data is just a proxy for control." Indeed, while UPS's director of process management Jack Levis said last year that "big data doesn't mean much" and that he really cares about "big impact," the biggest impact seems to be on UPS workers--who are increasingly pushed to work faster and longer.
YET LOGISTIC workers have shown that when they use it, they have enormous economic and political power.
The International Longshore and Warehouse Union (ILWU) is a case in point. In May, the contract between the ILWU and the Pacific Maritime Association, the major employers association, expired. Over the next nine months, the union and employers association fought back and forth. The Los Angeles Times captured the unique power of the dockers in the battle:
The dispute that has snarled West Coast shipping revolves around a rarity in American business--a small but mighty union. The International Longshore and Warehouse Union represents 20,000 dockworkers, a fraction of the organized ranks of teachers, truck drivers or healthcare workers. But the port workers--who still queue up at hiring halls daily for work and spend years earning full membership--stand guard over a crucial chokepoint in the global economy.
The fight also showed the union's limitations. Even though the job actions cost the U.S. economy billions of dollars and backed up the supply chain for months, the final agreement included serious union concessions.
What happened? A central problem is that the enormous power of the dockers is being slowly eaten away by the massive nonunion economy that surrounds the waterfront. The West Coast dockers "stand guard over a crucial chokepoint," but once you pass through, vast swathes of the logistics industry are nonunion, with workers laboring in terrible conditions.
For example, a 2010 study commissioned by the Warehouse Workers for Justice found that while there were more than 200,000 warehouse workers in Will County, an area southwest of Chicago where the logistics industry is burgeoning, they were not only largely nonunion, but 63 percent were employed by temp agencies.
AMALGAMATION--WHEN workers in small unions combine into one industrial union representing a particular industry--is as relevant today as ever before and should be the goal of any revived organizing in the sprawling logistics industry.
Important parts of the logistics industry are already unionized, such as UPS, USPS, DHL, FedEx pilots, dockers, and many railroad workers, and they should be the springboards for organizing the rest of the industry. The Teamsters are especially well positioned to launch logistics organizing, and the 60,000 UPS package drivers should be an invaluable resource to organize FedEx. But this potential army of organizers is neither inspired nor mobilized.
Amazon's chain of warehouses--which it has constructed across North America with the help of generous tax credits--is an obvious target for a major unionization campaign. The Teamsters and the ILWU have organized and represented warehouse workers for more than 80 years, and the working conditions in Amazon's warehouses, both in the U.S. and abroad, are notoriously bad.
After conducting an investigation that included interviews with 20 current employees at Amazon's Breinigsville, Pennsylvania, warehouses, the Allentown Morning Call summarized its findings in a 2011 article:
Workers said they were forced to endure brutal heat inside the sprawling warehouse and were pushed to work at a pace many could not sustain. Employees were frequently reprimanded regarding their productivity and threatened with termination, workers said. The consequences of not meeting work expectations were regularly on display, as employees lost their jobs and got escorted out of the warehouse. Such sights encouraged some workers to conceal pain and push through injury lest they get fired as well, workers said.
These working conditions cry out for action. While many Amazon warehouse employees work for third-party labor services that have been historically difficult to organize, a National Labor Relations Board ruling in late August made it legally easier to organize workers who labor under such exploitative arrangements. And workers outside the U.S. have already been pressing Amazon with workplace actions. Last December, 10 days before Christmas, 2,000 Amazon warehouse workers in Germany went on strike for better pay and working conditions.
As for the Teamsters, at its 2002 convention, General President James P. Hoffa declared, "We will set the course of our union into the 21st century." The course that Hoffa has set has been largely concessionary, and his organizing is even less inspiring. The largest victory in recent years was the 20,000 correctional, probation and parole officers with the Florida Department of Corrections (FDOC), which joined the union in 2011. "This is a great day for Teamsters," Hoffa boasted.
But FDOC absorption was more akin to old-fashioned raiding than organizing, and what it has to with building the union's strength in the logistics industry is anybody's guess. Meanwhile, the small local efforts carried out by Teamsters locals at FedEx Freight have been few in number, and a mixed bag of victories and defeats.
THE TEAMSTERS' 1997 UPS contract campaign and strike remains the model for organizing, educating, mobilizing, and leading a nationwide workforce into battle against a wealthy and politically connected logistics giant. The campaign provides valuable lessons for contract campaigns with existing employers and organizing nonunion logistic companies across the country.
The success of the campaign may also explain why there has been such a great effort to erase it from the public memory. Two of the major biographies of the era, Bill Clinton's My Life and Hillary Clinton's Living History, make no mention of the UPS strike or, for that matter, union leader Ron Carey or the Teamsters--despite the prominence of all three in the late 1990s. This deliberate act of political amnesia extends to the Teamsters, who, despite celebrating the strike on appropriate occasions, haven't leveraged the victory to launch new campaigns.
Carey told Labor Notes' Mark Brenner in 2007, "The labor movement has to grow, but it cannot attract new members when you are selling out the ones you have." While the Teamsters have the potential to be the central players in organizing the continent-wide logistics industry, it is difficult to see that happening with the current union leadership. On the other hand, a revitalized Teamsters union initiating a Fight for $15 campaign at UPS could mobilize the type of membership and community support needed to organize the entire logistics industry.
First published at Jacobin.